Apr 9, 2024 | News
In the dynamic world of industrial valves, butterfly valves emerge as the versatile maestros of fluid control. Amidst this symphony of options, three star performers take the stage: the Double Flange Butterfly Valve, the HP Butterfly Valve, and the Lug Type Butterfly Valve. Each valve dances to its own rhythm, offering a bespoke blend of features and advantages crafted to meet distinct needs. Let’s embark on a journey to unravel their unique melodies.
Double Flange Butterfly Valve

Imagine a valve with flanges on both ends – that’s the Double Flange Butterfly Valve. These flanges make it a breeze to install between existing flanges in pipeline systems. Not only does this design boost stability, but it also ensures a snug fit, preventing any pesky leaks or unexpected movements during operation.
Key Points:
- Simple installation thanks to flanges on both ends.
- Uses resilient seating materials like EPDM, NBR, or Viton for effective sealing.
- Often seen in applications that demand tight shut-off and minimal pressure drop.
Common Applications:
- Water treatment facilities
- HVAC systems
- Municipal water networks
High-Performance (HP) Butterfly Valve
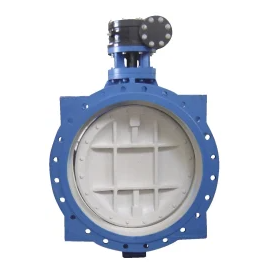
If you’re dealing with high pressures and temperatures, the HP Butterfly Valve is your go-to. Designed to handle tough industrial environments, this valve boasts a sturdy build and superior sealing capabilities, making it a reliable choice where performance is non-negotiable.
Key Points:
- Built tough to withstand high pressure and temperature conditions.
- Metal-seated design for extra durability and resistance to wear and tear.
- Can seal in both directions, providing flexibility in flow control.
Common Applications:
- Petrochemical plants
- Oil and gas pipelines
- Power generation plants
Lug Type Butterfly Valve
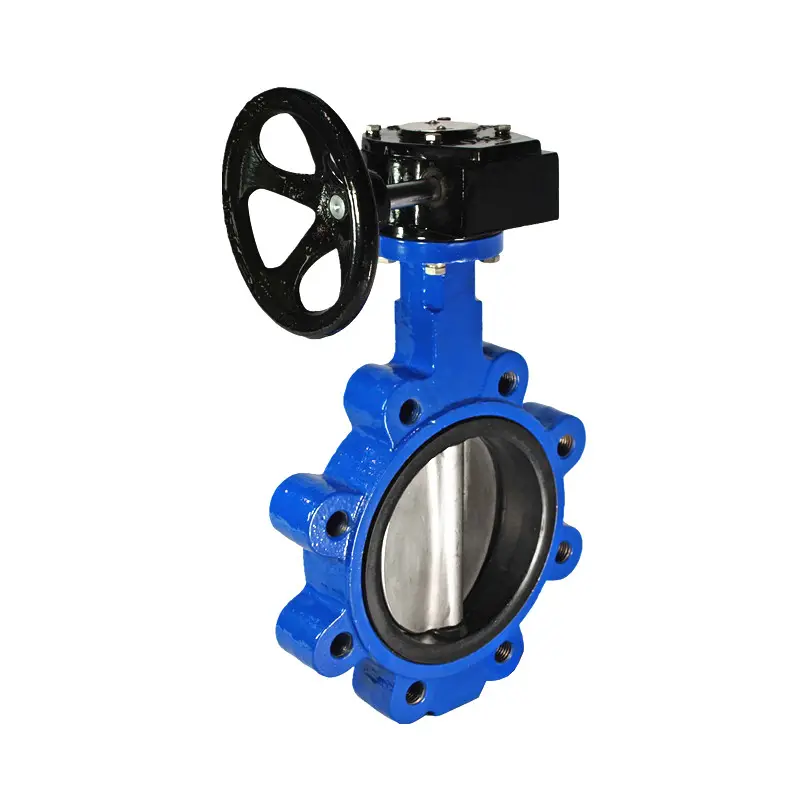
Ever needed to remove a valve without disrupting the entire pipeline? Enter the Lug Type Butterfly Valve. With its distinctive lugs or ears sticking out from the valve body, this type offers hassle-free installation and removal, perfect for situations requiring frequent maintenance or replacement.
Key Points:
- Lugs make for easy installation and removal without disturbing the pipeline.
- Available in both wafer and lug configurations for versatile installation options.
- Suitable for applications that need bi-directional flow control.
Common Applications:
- Chemical processing facilities
- Pulp and paper mills
- Water distribution systems
Comparing the Three
- Though all three types of butterfly valves share the same goal of controlling fluid flow, they differ in design, construction, and ideal applications.
- Installation: the Double Flange Butterfly Valve gracefully nestles between flanges, ensuring a snug fit that spells stability and security. Meanwhile, the Lug Type Valve takes a different approach, utilizing its lugs to effortlessly hook into place, offering a seamless removal process that keeps the pipeline undisturbed. It’s a choreographed dance of precision and convenience, each step orchestrated to perfection.
- Pressure and Temperature Handling:the HP Butterfly Valve emerges as the undisputed champion, capable of braving the fiercest conditions with unwavering poise. Its robust construction and advanced design equip it to tackle extreme pressures and temperatures, rendering it the hero of the most challenging industrial battlegrounds. It’s a testament to resilience, a beacon of strength amidst the heat of adversity.
- Sealing Mechanism: While all three types use resilient materials for sealing, the HP Butterfly Valve often incorporates metal seats for added durability in harsh conditions.
- Application Specifics: Each valve type is tailored to specific needs based on factors like pressure, temperature, and maintenance requirements. For instance, the Double Flange Valve is commonly found in water distribution, while the HP Valve thrives in industries with tough operating conditions.
At its core, selecting the perfect butterfly valve becomes a journey of discovering the harmony between your unique requirements and the valve’s capabilities. Whether you seek the seamless embrace of effortless installation, the stalwart resilience against the tempest of extreme conditions, or the comforting embrace of simplified maintenance, rest assured, there exists a butterfly valve tailored precisely to your needs. It’s a symphony of compatibility, where every note resonates with the melody of your specific circumstances, ensuring a harmonious flow in every aspect of your operation.
Apr 7, 2024 | News
Both pneumatic actuator butterfly valves and electric pneumatic butterfly valves present distinct benefits concerning control, velocity, and cost-effectiveness. Pneumatic variants, renowned for their automated actuation, are extensively employed across diverse industries. Conversely, electric actuators afford meticulous control tailored to particular applications.

Pneumatic butterfly valves are essential components in various industrial applications where precise fluid flow control is crucial. Here’s what you need to know:
Working Principle:
A pneumatic butterfly valve comprises a central disc nestled between a stem and a pipe. The stem links to a pneumatic actuator powered by compressed air, propelling either a diaphragm or piston. By rotating the stem 90 degrees, the actuator positions the disc parallel to the fluid flow, facilitating seamless passage through the valve. Rotating the stem partially enables proportional or throttled flow, making these valves suitable for modulating services.
Types and Applications:
- Concentric Type: These valves have a concentric disc closure design.
- Eccentric Type: Eccentric butterfly valves are also common.
- Connection Varieties: Valves are available in wafer-style, lug-style, or flanged designs.
- Utilizations: Pneumatic butterfly valves are applied across a spectrum of industries, encompassing chemical processing, water treatment, and HVAC systems.
Pros:
- Fast Response: Pneumatic actuators can quickly open or close the valve, making them suitable for applications requiring rapid adjustments.
- Cost-Effective: Pneumatic systems are generally more affordable than electric ones.
- Simple Design: These valves have fewer components, making maintenance and installation straightforward.
- High Pressure Handling: Pneumatic actuators can handle high-pressure environments effectively.
Cons:
- Air Supply Dependency: Pneumatic valves rely on a continuous supply of compressed air. Any interruption can affect their operation.
- Restricted Accuracy: Attaining meticulous control or exact positioning can pose difficulties owing to the discrete manner of pneumatic actuation.
- Audible Disturbance and Vibrations: Operational noise and vibrations may arise from pneumatic systems.
- Increased Dimensions: Pneumatic actuators typically exhibit larger physical profiles in contrast to their electric counterparts.

Electric butterfly valves combine the benefits of both electric and pneumatic actuators. Here’s a brief comparison:
Electric Actuators:
Utilize electrical power for precise control and automation.
Ideal for applications requiring accuracy.
Slower response time compared to pneumatic actuators.
Pneumatic Actuators:
Use compressed air or gas for actuation.
Faster response time.
Commonly used for larger valves due to cost-effectiveness.
Pros:
- Accurate Management: Electric actuators enable precise adjustment and meticulous control over valve opening and closing.
- Streamlined Processes: Electric valves seamlessly integrate into automated setups, minimizing the requirement for manual intervention.
- Independence from Air Supply: Electric actuators operate autonomously without dependence on external air sources, circumventing concerns related to air supply.
- Quiet Operation: Electric systems operate quietly without the noise associated with compressed air.
Cons:
- Slower Response: Electric actuators are generally slower to respond compared to pneumatic ones.
- Higher Cost: Electric systems tend to be more expensive upfront.
- Complexity: Electric actuators have more components, which can increase maintenance complexity.
- Limited Pressure Handling: Electric actuators may not handle extremely high pressures as effectively as pneumatic ones.
In summary, choose based on your specific application requirements. Pneumatic actuators excel in speed and cost-effectiveness, while electric actuators offer precision and automation capabilities. TWT Valve is a professional manufacturer from China can produce pneumatic actuator butterfly valve, electric pneumatic butterfly valves, and ductile iron wafer butterfly valve.
Apr 7, 2024 | News
Check valves are essential components that serve to prevent reverse flow within a system. Their primary function is to facilitate fluid movement in a singular direction, automatically shutting off when there’s an attempt of fluid movement in the opposite direction. This article will explore three distinct types of check valves, each offering its own set of features and benefits.
Axial Flow Check Valve
Axial Flow Check Valves are pivotal for the protection of pumps and compressors. They induce flow in one direction and prevent backflow in the other. This results in reduced extensive damage to equipment, increasing system durability. The benefits include rapid closing, tailored sizing, a compact design, and substantial flow coefficient, making them the ideal valve for oil collection and transmission. Apart from their responsiveness to change in flow, they also have a low maintenance cost, making Axial Flow Check Valves a suitable addition to various industries.
Dual Disc Check Valve
Dual Disc Check Valves, alternatively referred to as Double Door Check Valves, exhibit versatility and extensive application across various sectors including water treatment plants, oil and gas refineries, chemical processing plants, and power generation facilities. Renowned for their efficacy in fluid and gas regulation within these industries, their design minimizes downtime, bolsters safety measures, and enhances overall reliability. Particularly suitable for scenarios demanding minimal pressure drop and the prevention of potential leakage issues, this non-slam valve stands out for its performance.
Stainless Steel Check Valve
The rising popularity of Stainless Steel Check Valves stems from their remarkable combination of strength, durability, corrosion resistance, and precision. Their widespread adoption in demanding environments like food processing, pharmaceutical manufacturing, and petrochemical industries underscores their robustness. Stainless steel’s innate corrosion resistance ensures these valves withstand water and harsh chemicals exceptionally well, enhancing their versatility and widespread use.

Axial Flow Check Valves, Dual Disc Check Valves, and Stainless Steel Check Valves offer distinct advantages and are suited for specific applications. Appreciating the nuanced disparities between these valve types can significantly aid in their appropriate selection, especially when seeking optimal functionality to meet various system demands.
In this article, we explore the distinctive applications and benefits of various check valves, particularly axial flow check valves, dual disc check valves, and stainless steel check valves. Understanding these differences can help inform better decisions when selecting a check valve for various uses.
Apr 7, 2024 | News
Delve into key attributes of high-performance butterfly valves meticulously crafted to fulfill the stringent requirements of vital applications, emphasizing reliability, precise shut-off capabilities, and enduring durability.
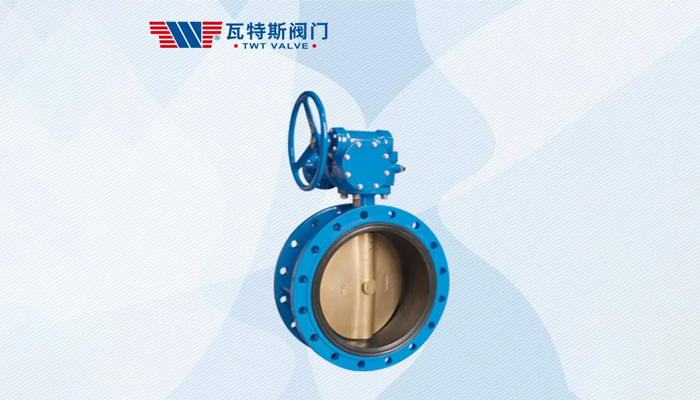
Design and Operation:
The valve consists of a disc, often referred to as the “butterfly,” positioned perpendicular to the flow direction. This disc is connected to a shaft, enabling rotation for flow regulation. Soft-sealing butterfly valves utilize a soft seal, typically made from rubber or elastomer, to ensure a tight shut-off and minimize the possibility of leakage.
Applications:
These valves find use in various industries:
- Chemical Processing: Demonstrates exceptional resistance against corrosive fluids.
- Water Treatment: Frequently employed to regulate water flow within treatment facilities and distribution networks.
- HVAC Systems: Manages air and water flow within heating, ventilation, and air conditioning setups.
- Food and Beverage: Incorporates a hygienic design tailored to the requirements of the food industry.
- Power Generation: Exercises control over water, steam, and various fluids within power plant environments.
Advantages:
- Cost-effective: Generally more affordable than other valve types.
- Compact design: Lightweight and easy to install.
- Quick operation: Quarter-turn action enables fast opening and closing.
- Tight shut-off: Soft sealing ensures minimal leakage.
- Low maintenance: Simple design with fewer components and long service life.
When selecting a soft sealing butterfly valve, consider factors such as operating conditions, size, and flow capacity to ensure optimal performance.
Design and Operation:
The valve comprises a disc, commonly known as the “butterfly,” affixed to a valve stem. This stem extends through the valve body and links to an actuator or handle. Upon turning the actuator or handle, the disc rotates, either permitting or obstructing the flow. Its double-flanged design entails flanges welded to both the inlet and outlet ends of the valve body.
Applications:
These valves are frequently employed to control, regulate, and throttle the flow in diverse applications across industries such as water treatment, chemical processing, and HVAC systems.
Advantages:
- Resilient Seating: The double-flanged design ensures a tight seal, making it suitable for dead-end service.
- Easy Installation: The flanges allow straightforward connection to pipelines with matching flange sizes.
Remember, double-flanged butterfly valves are versatile and reliable components used in fluid systems for efficient flow control.
Design and Operation:
A double-offset butterfly valve is designed with two key offsets compared to the concentric type:
- First Offset: The shaft is not centered on the disc but positioned slightly behind it. This arrangement creates a continuous sealing surface on the disc.
- Second Offset: The shaft is not aligned with the pipe centerline but is slightly to the right of the center. When fully open, the valve doesn’t touch the seat at all. This reduces friction compared to concentric valves and prolongs the seat’s lifetime. The 90° rotation of the disc ensures efficient flow control.
Double-offset valves are used in systems requiring higher pressure resistance.
Applications:
Control flow in pipelines, tank farms, and refineries.
Handle crude oil, natural gas, and other hydrocarbons.
Used in cooling water systems, steam lines, and fuel handling.
Resistant to high temperatures and pressure fluctuations.
Regulate air and water flow in heating, ventilation, and air conditioning systems.
Efficient for maintaining comfort levels.
- Food and Beverage Industry:
Handle food-grade liquids in breweries, dairies, and beverage production.
Installed in ballast systems, cooling circuits, and fuel lines.
Resistant to saltwater and marine environments.
Resistant to chemicals and pulp slurries.
- Steel and Metal Processing:
Handle high-temperature gases and molten metals in steel mills and foundries45.
Advantages:
- Higher Pressure Resistance: Double-offset valves offer up to a Class 600 ANSI rating in materials like stainless steel, carbon steel, and Hastelloy.
- Reduced Operating Torque: Easier to open and close due to lower torque requirements.
- Increased Flow Capacity: Boasts better flow capacity compared to other valve types.
- Ease of Cleaning: Much easier to clean than gate valves, improving worker efficiency.
- Compact and Lightweight: Weigh less and occupy less space than other valve types.
- Longevity and Durability: Suitable for extreme conditions, such as gas pipelines and offshore oil rigs. Adds longevity to different systems and reduces maintenance tasks
Apr 6, 2024 | News
A non rising stem resilient seated gate valve is a type of valve commonly used for controlled shut-off in fluid distribution systems. Let’s break down its key features and applications:
Construction and Operation
Gate valves operate using a wedge-shaped disc that moves linearly to open or close flow paths.
Resilient seating improves sealing compared to metal-to-metal designs. It incorporates an elastomeric “O-ring” around the disc edge, which compresses against the valve body for a drip-tight shut-off. This design ensures that irregularities in the pipeline do not affect the sealing.
In non-rising stem gate valves, the stem is threaded separately from the gate. As you turn the handwheel to open or close the valve, the gate rises and lowers, but the stem itself does not move up or down. This design maintains a compact envelope and prevents stress during buried service.
Valve Standards
These gate valves adhere to stringent specifications, ensuring interchangeability and quality assurance. For buried potable water, they follow standards like AWWA C509, while for aboveground service, they adhere to AWWA C515.
Compliant valves undergo hydrostatic shell testing, seat leakage acceptance, and operational durability verification. They maintain drip-tight sealing over millions of cycles.
Suitable Applications
Resilient seated gate valves find application in various scenarios:
- Municipal Water Transmission/Distribution: They play a crucial role in water supply systems.
- Industrial, Commercial, and Building Services: Mild industrial applications benefit from their robust performance.
- Isolating Pipelines: During maintenance or repairs, these valves help isolate sections of pipelines.
- Throttling Flows: They allow flow control within a system.
- Downstream Equipment Protection: By shutting off flow, they safeguard downstream equipment.
- Emergency Sectionalization: In emergencies, locating remotely, they can isolate specific parts of the system.
Installation Considerations
Proper installation factors in pipe stresses, substrate, operation loads, and accessibility for future maintenance.
Compact joints, thrust blocks, and trench design address installation loads.
Valves are oriented to position actuators above grade or indoors, avoiding joints within casing intervals.
External coatings and lining protect against corrosive contents and harsh environments.
Maintenance Practices
- Routine exercising and inspections catch early signs of minor leakage, allowing proactive O-ring replacement.
- Flushing before repairs removes debris that could damage sealing interfaces.
- Repair “kits” simplify barrier replacements during infrequent shutdowns.
- Cathodic protection retards corrosion if electrically isolated.
- Proper handling protects seal materials during joint assembly.

The relationships with other types of gate valves
A non-elevating stem gate valve belongs to a category of gate valves distinguished by the stem, which remains fixed in its position while the valve is in operation. When you manipulate the handwheel to either open or close the valve, the gate, located within the valve, moves vertically, while the stem remains immobile. Such valves find frequent application in scenarios where spatial constraints are present, such as underground setups or environments with limited accessibility. The sealing mechanism may entail either a metal-to-metal interface or a resilient design featuring an elastomeric seat.
A resilient-seated gate valve is distinguished by its elastomeric seat, which offers superior sealing capabilities. Featuring a groove encircling its edge, the gate employs an O-ring or similar resilient material that compresses against the valve body upon closure. These valves are particularly well-suited for applications demanding a secure seal, notably in water distribution systems. Resilient-seated gate valves may adopt either a rising stem configuration, where the stem ascends and descends, or a non-rising stem design, where the stem remains fixed in place.
In summary, non-rising stem resilient seated gate valves deliver highly reliable shut-off, backed by robust engineering. They are essential components in water infrastructure worldwide.